PRO S
Your profiling line for high capacity
If you are looking for an economical sawline with high production capacities, the profiling line PRO S perfectly meets your requirements. With the profiling technology invented and developed by LINCK, its automatic log rotation, its diagonal alignment and sideboard optimization, the sawline converts logs into high-quality centre products and sideboards. Like with every LINCK sawline, we also adapt the profiling line PRO S exactly to your requirements.
Key data
- Processing up to 400.000 m³ of round logs per year and shift
- Feed speed from 40 to 200 m/min and more– depending on the configuration
- Operating mode: processing of sorted logs
- Log diameter, large end, up to 60 cm
- Log diameter, small end, 10 cm
- Log length 2,50 to 6,20 m
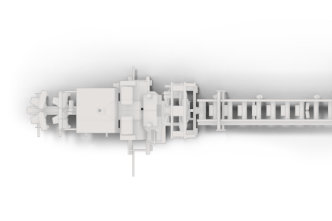
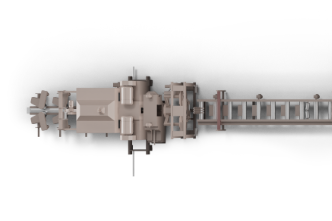
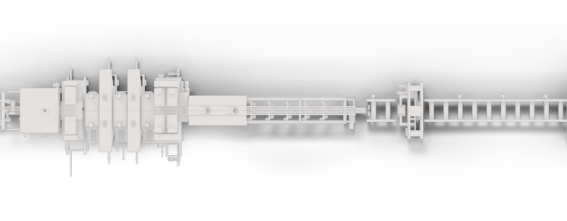

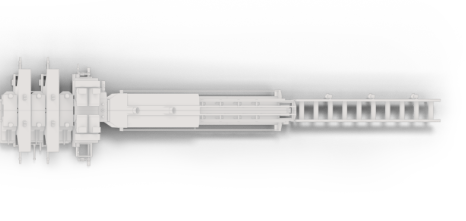
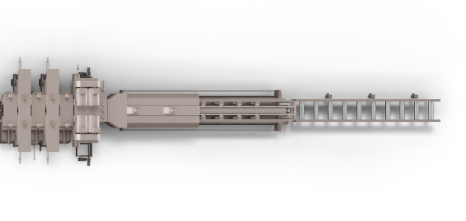